Performance increase unlocks two value creation pathways
Achieving the same with fewer resources
Reduce weight and maintain the properties
Our patented processing technology leverages advanced polymer rheology science to optimize the functional performance of materials, allowing us to reduce material usage while maintaining critical properties. This means achieving the same product performance with fewer resources, offering significant cost savings and sustainability benefits.
Among those benefits:
Reduce transportation costs
Maintain top load mechanical strength
Maintain barrier and thermal properties
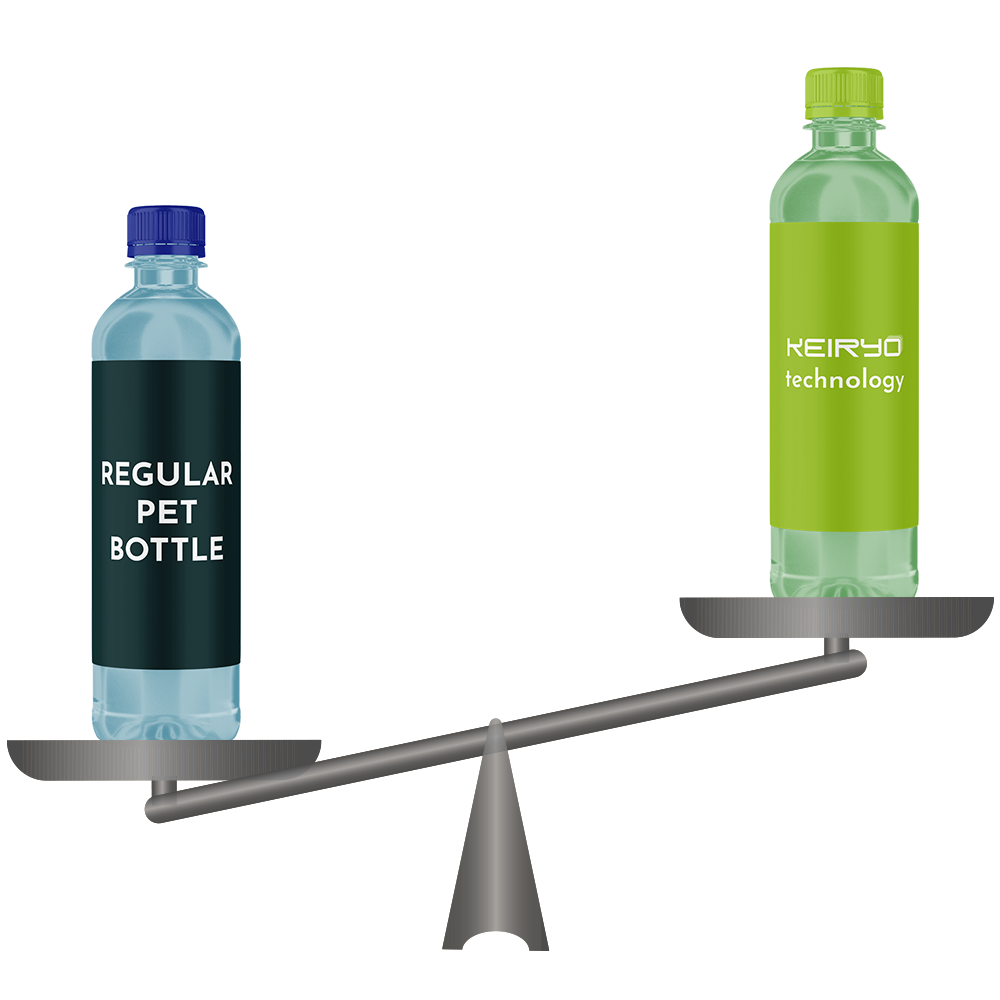
Achieving more with the same resources
Maintain the weight and increase the properties
KP processing technology enables to maintain material weight while significantly enhancing its functional performance.
Among those benefits:
Enhance barrier properties
Increase mechanical strength
Improve thermal properties
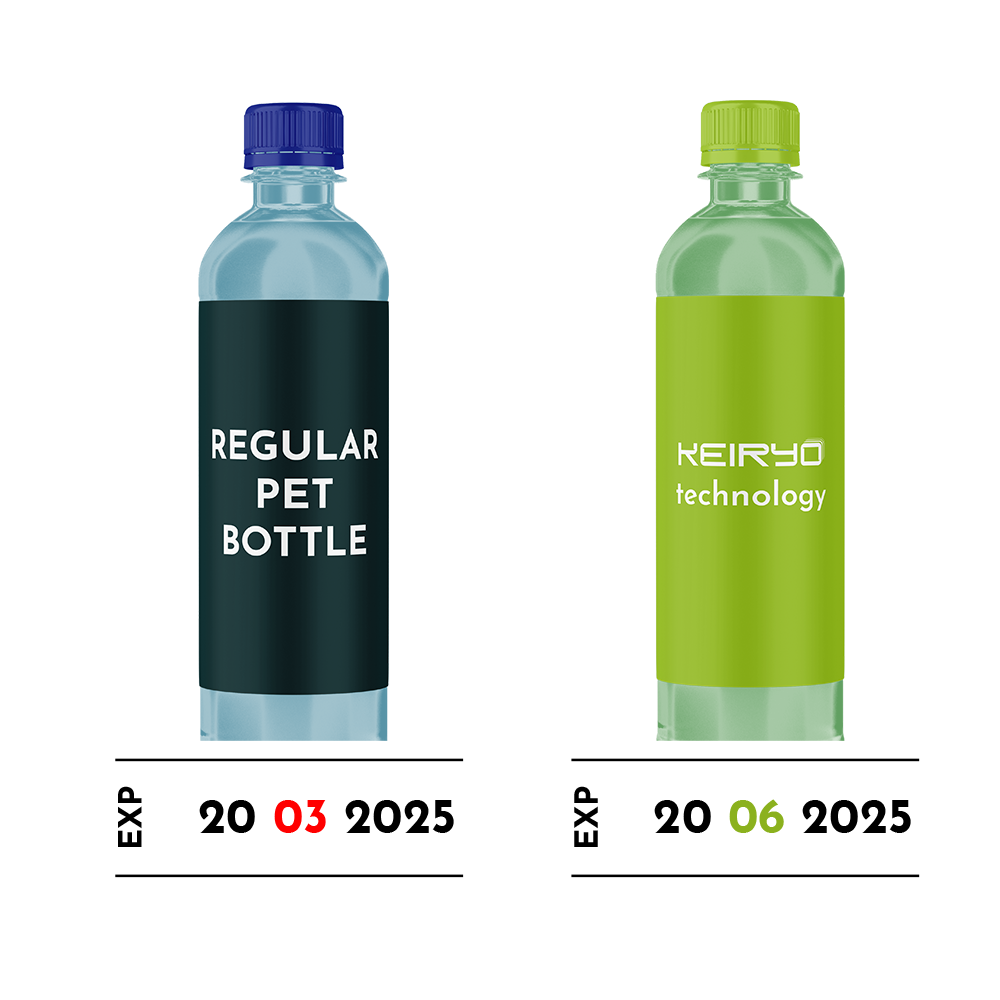